The challenge
Cast iron cylinder liners are required in lighter-weight aluminium engine blocks to provide a hard wearing surface for pistons. To ensure there is no movement of the liner during engine use and to provide good heat transfer away from the combustion zone, the aluminium block is cast around a cast iron cylinder liner that has a textured external surface. However machining grooves into the liner’s surface to achieve this texture is an expensive process.
Our solution
Foseco has developed a process using proprietary coating technology and centrifugal casting to produce liners with a textured surface that allows molten aluminium to flow easily around it – even when using low pressure or gravity die casting – whilst providing a secure interface with the solidified aluminium.
The benefits
This solution creates value for the customer by eliminating costly cylinder liner machining. Additionally these liners can be used for both low pressure and gravity die casting, enabling manufacturers to maintain the cost benefits associated with as-cast liners whilst moving to rigid closed-deck engine designs. This can lead to an overall weight reduction and allow increased combustion temperatures and pressures which improve vehicle fuel efficiency and reduce emissions.
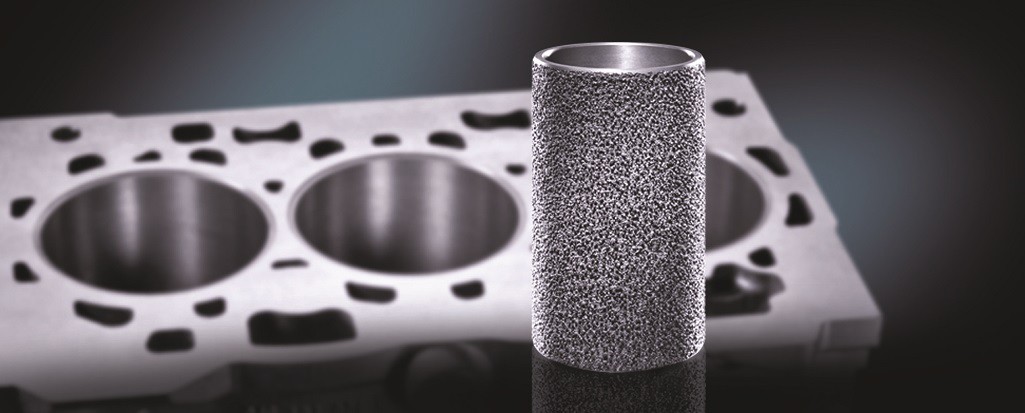