The challenge
Controlling the flow pattern of molten steel as it enters the mould is critical to achieving the highest quality standards in steelmaking.
The complexity of accurately monitoring these flows makes the development of efficient solutions to problems of product quality and of productivity particularly challenging.
Our solution
AVEMIS, a company in the Technical Services business of our Steel division, has developed the XMAT concept.
The XMAT device is an ‘expert eye’ in the mould. It includes advanced instrumentation for capturing data and, for the first time in continuous casting, it is now possible to measure and record the slightest deviation in flow pattern, sub-meniscus velocity, molten steel temperature and mould level on either side of the entry nozzle.
The data captured from these measurements, combined with the analysis performed by our technical experts, enables us to identify issues and optimise the steel casting process.
The benefits
By delivering this combination, the XMAT device helps to monitor production, influencing the process of solidification and the quality of the final steel slab. Over the longer term the data from the XMAT device measurements will provide customers with a deep and accurate source of knowledge about their process, enabling them to anticipate future requirements and develop solutions.
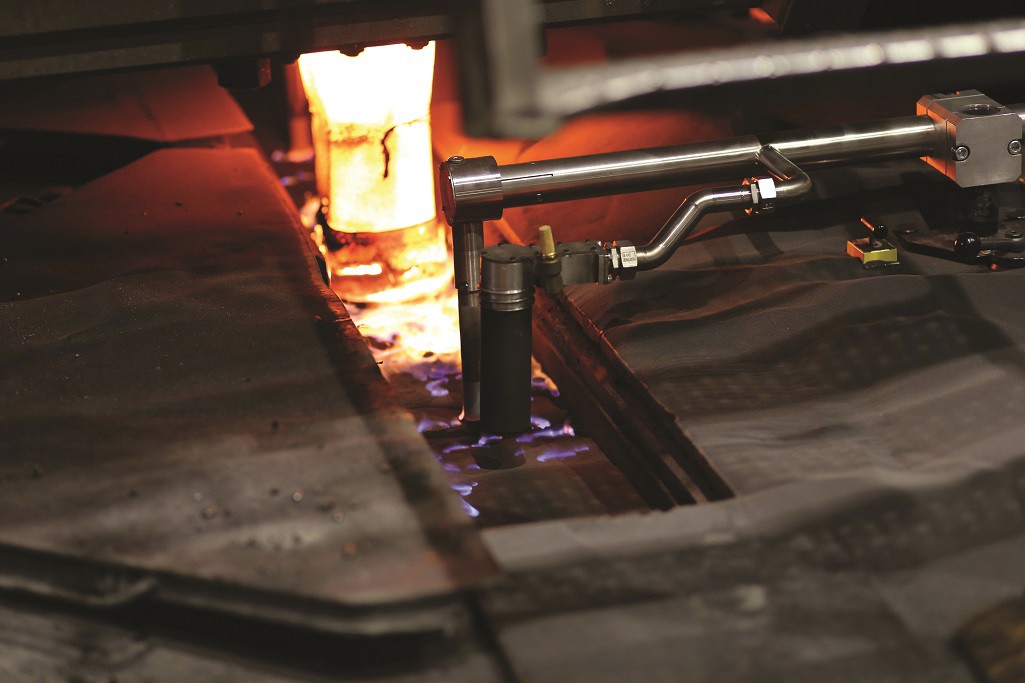