The foundries will stand up to new challenges and solve the problems
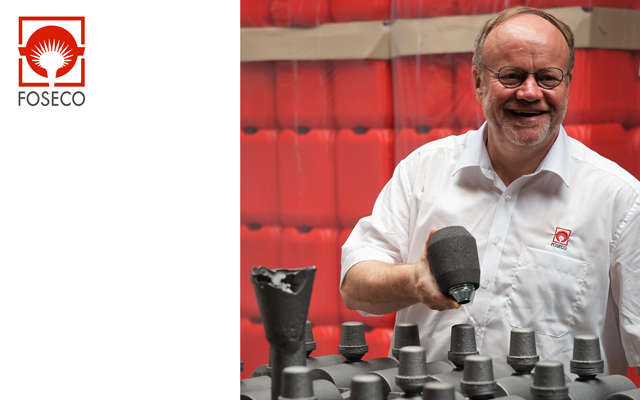
What can visitors expect from the upcoming GIFA trade show? What will be different compared to last GIFA in 2015?
The megatrend of the moment and the topic of the future in production technology is additive manufacturing. Also the digital transformation is an issue for foundries. 3-D printing has been gaining in importance alongside traditional manufacturing techniques. 3-D printing has already proved its worth in practice in a wide range of high-end sectors such as in medical engineering as well as in the automotive and aerospace industries. Meanwhile also the foundry industry and the steel and aluminium sectors have recognized the potential of 3-D printing. GIFA is going to dedicate due attention to this topic, among others by a special show featuring the great potential this technology provides. I am sure that we will see 3-D solutions and products not only at the special show, but also at numerous exhibitor stands. We are very likely to come across exciting approaches to designing self-optimizing systems as part of the “digital transformation”.
Who should visit GIFA?
Everybody active in the foundry industry or in related sectors should see GIFA as an opportunity to get a personal impression of the state of the art and current development trends. The main target groups of GIFA are employees and managers of iron, steel and malleable iron foundries, as well as non-ferrous metal foundries. The trade show also addresses mechanical and apparatus engineering companies and manufacturers of equipment for the automotive and gear engineering sectors as well as the supply industry.
Recent development trends like 3-D printing and digital technology are characterized by much shorter innovation cycles than those we know from classical foundry equipment suppliers. Competitive events such as the biennial Euroguss become bigger and more international, and new trade fairs with new focuses, like CastForge in Stuttgart, have emerged. How is GIFA positioned within this competitive landscape?
Events with a regional or national scope fulfill an important role, as they cover topical issues from the expert angle and address a regional audience. However, GIFA – and METEC, THERMPROCESS and NEWCAST alike – showcase innovations, products and services on a global scale. No other trade show provides such a wide-ranging and far-reaching picture of the complete range of foundry technology, cast products, metallurgy and thermal processing technology. It is a forum for both the big players of the foundry industry and the smaller, highly innovative champions to present themselves to large audience. The big equipment suppliers often time their research and development projects around the fouryear cycle of the show. The key to the success of this trade fair quartet is that it covers the complete market of both the demand and supply side. This also mirrors in the decision-making responsibility represented by the GIFA visitors: In 2015, more than half of the about 50,000 visitors held top management positions and correspondingly high decision-making responsibilities. In terms of internationality, the trade fair quartet GMTN is second to none: In 2015, 58% of the visitors came from 112 different countries. And the fouryear cycle ensures that the event does not loose any vigour.
Is it true that apart from new topics such as additive manufacturing and the digital transformation the overall concept of the fair has remained the same?
Obviously GIFA comes up to the visitors’ expectations. For example, in 2015, 97% of the about 50,000 visitors gave a very high rating to the event and stated that their expectations had been fulfilled. Every second one stated that they had established new supplier relations. GIFA is certainly an ideal platform to meet customers, colleagues and junior staff. We expectyoung talent to visit the trade show in great number again next year.
In which way has the economic landscape changed versus 2015?
A key criterion for the assessment of the foundry market is the cast output. NF-metals foundries have seen a constant rise in production and, with lightweight construction and e-mobility gaining in importance, their prospects for the future are also excellent, especially in pressure and low-pressure die casting ...
But not for the iron foundries ...
... the iron foundries in Germany – and elsewhere in Western Europe – experienced a rather moderate development from 2011 until recently. However, since 2017 and the first half of 2018, they have been feeling a clear upturn. This was triggered by the growing demand in the mechanical engineering sector as a result of a catch-up effect and a booming phase in all its subsegments, with the exception of wind power. Although the current market situation is very positive, there is a dark cloud on the horizon. This is due to the dramatically changing eco-political environment. Just take the anti-free trade measures implemented by the US Administration, the unsolved Brexit or the increase in sanctions. The reliability of business relations has definitely not improved. Let’s hope that the all in all positive climate will persist beyond next year’s GIFA.
What will be the main top issue at next GIFA?
I do not see one single, overwhelming topic, but several interrelating and interdependent issues. As well as additive manufacturing, topics like lightweight construction in automotive engineering, Industry 4.0, the digital transformation, energy and resource efficiency, and sustainability will play central roles at next GIFA – not forgetting e-mobility.
Do you see additive manufacturing and casting as partners or competitors?
They are two complementary trends. Generative processes currently represent one of the most important and intensive research areas of the global industry. Products for specific applications, prototypes and parts for airplanes are already being produced by 3-D printing, replacing castings in these areas. However, for large series production, casting still is the most economical process – also according to statements by major OEMs. With computers becoming increasingly more efficient and faster, costs decreasing and the quality of metal powders improving, this balance may, however, slightly shift towards 3-D printing in the future. There are already examples of application where 3-D printing and casting complement each other. These will be featured in a special show at GIFA.
Is 3D printing also an interesting option for your company?
We already produce prototype tools by 3-D printing. This allows us to test the tools under manufacturing conditions before kicking off the cost-intensive production of metal tools in large series. We know that some pressure die casting shops use extremely complex tools which they can produce only by 3-D printing. Additive manufacturing provides much more design options, for example, as it can produce parts
with undercuts.
What will be Foseco’s main focus at GIFA?
Foseco is going to feature the main R&D areas in foundry technology. Energy and resource efficiency can be significantly improved by specific products and technologies. Visitors may look forward to our presenting innovations in gating technology. We will introduce a new technology allowing virtually turbulence-free casting of medium-heavy steel castings. In non-ferrous metals treatment, we have long been active in developing products and processes for optimized melt refining.
At our booth we will showcase new technologies for our FDU and MTS equipment in combination with innovative solutions for the metal transport. Innovative coating and binder systems will round out our exhibits.
Do you think there is potential for the casting process to substitute any of its competing manufacturing techniques? Do you expect any new casting solutions and new markets for castings to occur?
We are in competition with hybrid metal/metal and metal/plastics components, with 3-D printing, with high-performance machining techniques, and with our traditional “competitors” forging and welding. We don’t see the new technologies take over significant market shares from the foundries or vice versa during the next five years. However,
this does not mean that the new technologies will not position themselves in the market as solutions for certain niche applications or applications that require a very specific range
of properties. By further sophisticating the technology of thin-wall casting not only in pressure die casting but also in iron and steel casting, the foundries may open new application opportunities. Also the development of new casting materials and the further development of existing ones will provide new options. Generally, due to the advance of e-mobility, we will see a number of entirely new components in the market, mainly made of aluminium.
Yet, a growing mix of materials is being used in automotive engineering.
This further intensifies the competition between materials and production
processes. Are structural components made of fibre reinforced composite materials a threat to structural aluminium castings?
The plastics industry has been dedicating great efforts to achieving an even
deeper penetration of the automotive market. Thermoplastics and fibre reinforced
plastics are used in technologically highly demanding solutions. However, casting alloys, in the here described case especially high-strength aluminium alloys for the production
of safety-critical components, provide better strength and elongation properties.
Only casting alloys can be 100 percent recycled and reused to produce a casting of the same high quality. Plastics manufacturers still haven’t solved the issue of recycling. And the current discussion about plastics contaminating the environment is likely to serve as a promoter of cast products.
Are the players in the markets relevant and with a potential for castings aware of the advantages of cast products? Or is this an area where the foundry industry needs to become more active?
Our big customer segments are passenger car and utility vehicle producers and the mechanical engineering sector with its numerous subsegments. Alongside these, there are many more specialized segments. The main customer groups of the foundry industry know the advantages of castings very well. However, I believe that spreading the word about the foundries’ performance capacities more widely and intensively would open new application potential for castings also among our traditional customers. Despite the Internet, websites and search engines, the lack of knowledge about the performance features of cast components is surprisingly great in many potential customer segments. Nevertheless, the foundries should not start to take over the job of the universities.
Up until the present, iron castings have always succeeded in defending their position in automotive engineering against non-ferrous metals castings, even in lightweight solutions. Is this going to change in the future against the backdrop of e-mobility?
Weight reduction of castings for automotive applications will remain a key development target among OEMs, independent of e-mobility. We can see today that castings will continue to be indispensible in both fully electrically and conventionally propelled vehicles.
Lightweight construction with cast iron components, and with thinwalled steel castings, will also be needed in the future alongside further optimized solutions based on light-metal castings. Iron and steel castings owe their relevance to their excellent fatigue strength properties and the great flexibility in designing bionic constructions. The production of thin-walled iron and steel castings requires high capital investments in machinery, above all in core and mould making equipment, fettling machines, robotic equipment for automatic handling and, last but not least, machining systems.
Where do you see potential for steel casting?
We expect a great deal from steel casting. The last few years have seen a strong demand for lightweight castings, especially of ferrous materials. One can generally state that casting is an ideal process for bionic constructions. Here, we expect new opportunities for steel castings. Currently, thinwall casting of steel is being further developed with a view to new applications triggered by e-mobility but only feasible thanks to thin-walled steel castings. An example is the development of spring supports for chassis.
Should foundries get more involved with IT-related topics and new, data-driven business models?
Foundries are familiar with data-driven business models because many of their customers operate on this basis. The customers usually define the requirements and the foundries have to comply with them in due time. Every foundry should carefully consider up to which point it is willing to disclose their processes and operating procedures to their customers. There is no need to lay the entire production process open because there are other options.
In no way should the foundries adopt a defensive attitude. They are way ahead of many other industries and boast excellent skills and competences. For 5,000 years, progress has
been tradition in the foundry industry. And I am confident that the foundries will come up with exciting solutions in response to the digital transformation.
Is Industry 4.0 a chance for foundries?
In order to improve their competitiveness and make processes more consistent, foundries are urged to invest even more in automation and process control. There are concrete plans to build new foundries here in western Europe. These projects derive their profitability from much improved productivity, reduced maintenance needs and lower energy costs. This entails very high capital investment. But capital costs are low at the moment. Many foundries have reacted to the new situation and started to dedicate resources to making their operations more digital and smarter. The casting process is still held as being not fully controllable. Current computer capacities and the possibility to measure an increasing number of casting parameters and feeding them into process control loops via dedicated software programs opens many new opportunities.
Where in the foundry world will the most important developments in digital transformation take place?
Generally speaking, all activities in connection with customer relations will to an increasing degree be handled electronically and via the Internet. Designing, quotations, coordination of deadlines, meetings via Skype or video conferences – all this has become so much easier thanks to the highspeed Internet. And internally, there are digitized processes like simulations, patternmaking and, in the meltshop, charging and furnace control. Or let’s take the optimization of machine control in the core and mould making shops, in the fettling shop and, if applicable, in the machining area. Whether in the acquisition of operating data, quotation preparation and pricing, quality data collection and evaluation, in all these areas the use of Big Data and digital solutions will increase dramatically. In the future, many new foundry and casting parameters will be collected and fed back into the systems for process optimization. More and more robotic systems will be used in mould and core making, for fettling and machining operations down to the dispatch of the castings. In other words: in all process steps with a potential to control or reduce costs and make the processes faster and more consistent. Administrative procedures such as procurement and accounting are in many cases already digitalized to a high degree. Also after-sales services and the spare parts business will become more digital.
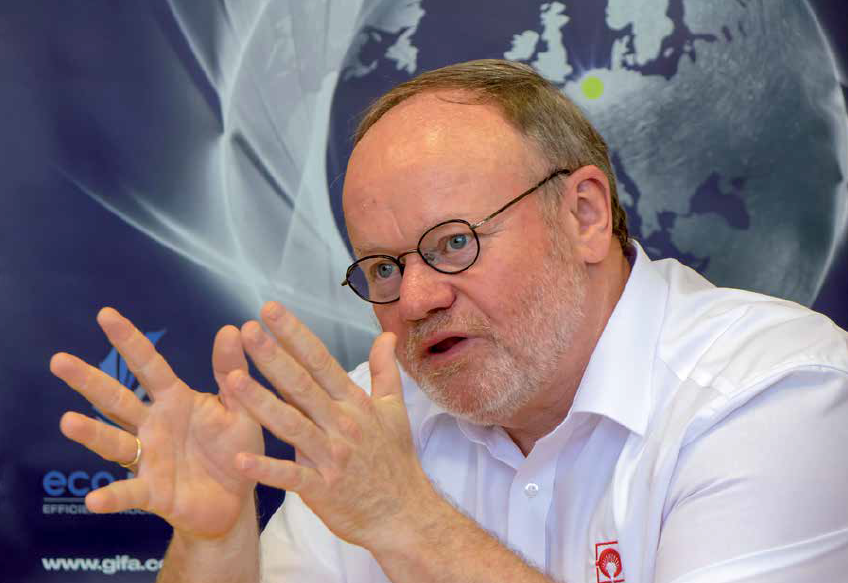
Are the classical business models in place in the foundries at stake due to digital disruption?
Looking back, there have been very few dispruptive developments. Therefore we should avoid calling every development a disruption or revolution. Especially the fact that most of the foundries are medium-sized businesses will allow them to quickly adjust to changing circumstances. The flexibility and agility are lived reality in our industry.
Don’t you think that the growing digitalization will change the working environment in the foundries?
Being a classical supply industry, foundries have always been extremely flexible in adjusting to customer wishes and deadlines. Communications technology has been advancing with rapid strides. The “new generation” of foundrymen has grown up with modern communication devices. Therefore it is normal for them to use them on the job. The foundryman of the near future will certainly control its moulding line via an app. We will see this happen very soon. But there is no reason to be concerned because: “A foundryman can handle everything!”
What new challenges will the foundries be confronted with in the future?
All kinds of challenges are possible: profitability, technology, customer relations, competition, environmental regulations, technophobia, human resources, regulation, and many more. And we will certainly also be presented with challenges that are unimaginable
today and that will come as a surprise. Not very long ago, nobody expected that we would so soon see trade barriers being set up everywhere in the world. No matter what challenges, the foundries will stand up to them and come up with solutions – worked out in cooperation with their customers and suppliers.
What do you think will be the biggest challenges for the foundries during the next five years?
Every company must be ready to permanently fight for their survival. There is often not one single front line, but a fight at many different fronts. As well as the economic constraints and the technological challenges, safeguarding a qualified human resource base will become increasingly important and mission-critical. The generational change in all areas of the foundries will lead to a shortage of skilled labour.
In your opinion, what is the currently the most exciting development in the world of casting?
Our industry can only prosper in the long run when we succeed in attracting and training foundry specialists of the next generation – now! Our trade associations BDG and VDG as well as universities and companies have undertaken great efforts to improve our industry’s image and make the foundry trade attractive for more young people. We see first positive results of this campaign. An increasing number of university graduates have followed the invitation to our annual foundry conferences in recent years. At next GMTN we will offer a special program for school students, giving them the opportunity to learn about the vast range of highly attractive technology- related jobs.
The interview with GIFA and NEWCAST President Heinz Nelissen was conducted by Gerd Krause, Mediakonzept, Düsseldorf, Germany.