Solutions for Ingot Casting
When steel is poured into the ingot mould, progressive solidification starts from the walls and the base of the mould, moving inwards towards the thermal centre or axis.
The liquid steel decreases in volume during and after solidification and there is insufficient solid metal to fill the shell first formed. The result is a body of steel with cavitation or in the region of the last metal to solidify. This is not the case with rimming steel where the shrinkage is compensated for by the formation of gas blowholes.
The severity and distribution of this, depends on several factors including the quality of steel, superheat at the time of pouring, method of pouring (whether direct or indirect) and the dimensions and taper of the mould. Such cavitation is also associated with impurities, which concentrate, by segregation forming an undesirable distribution of undesirable elements in the final product.
It is thus important to influence the amount and position of cavitation by reducing it to a minimum and locating it where it will be least harmful in the solidified ingot.
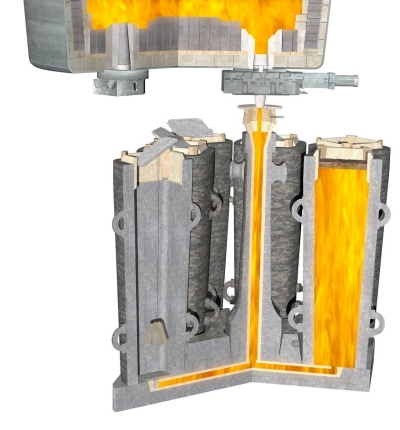
In order to achieve this VESUVIUS has a range of products and services aimed at reducing undesirable segregation and increasing the yield of sound steel in the final ingot. These products and services include:
Anti-piping compounds:
KALTOP* anti-piping compounds in board form
FERRUX* anti-piping compounds in board form
Casting flux:
STELOTOL* powder or granular casting flux
Heading systems:
KALMINEX* exothermic sleeves
KALMIN* insulating ingot heading tiles
LITEFAX* highly insulating ingot heading tiles
PROFAX* insulating lining sleeves and tiles