Controlling the flow of steel from the tundish to mould in a thin or medium slab caster is critical because of the high casting speeds combined with limited volumes and clearances in the mould.
Achieving the top steel quality and maximum productivity in thin slabs requires:
- a reliable flow control that guarantees a stable, level meniscus and safe casting
- an SEN design that guarantees the proper steel distribution into the mould and allows long cast times
- the appropriate high quality formulation and consistent distribution of mould flux
Vesuvius brings its skills and experience in thin slab to develop solutions for our customers that maximize production quality and throughput with the highest safety possible. The integration of Avemis, Sert Metal and Metallurgica enlarged the Vesuvius portfolio and experience in this field.
Shroud
VISOTM Shroud : Tundish to Mould shrouding
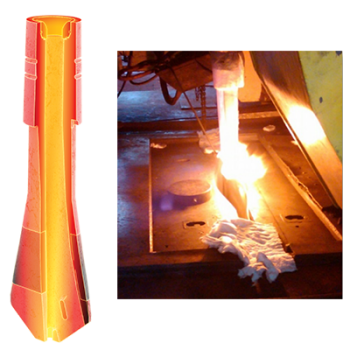
Primary function and objectives of the shroud:
- Controlled submerged introduction and distribution of molten steel from the tundish to the mould
- Prevention of reoxidation of the steel, and the formation of slivers, caster folds and other quality issues related to steel flow
Main features:
- Most commonly isostatically pressed tube (VISO™),
- High erosion resistance zirconia sleeve material for long casting time
- High thermal shock and oxidation resistance to accommodate various preheating conditions
- Optimized outside geometry design for suitable mould to nozzle clearance
- Optimized internal geometry design for optimum flow in mould
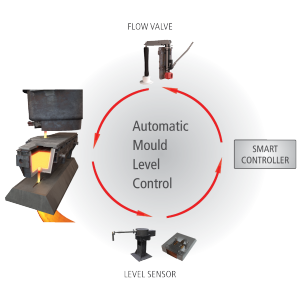
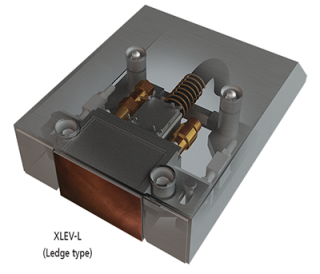
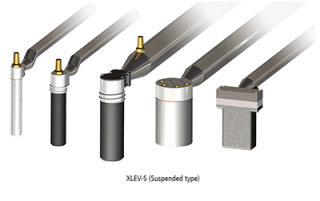
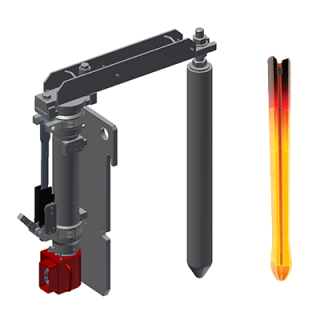
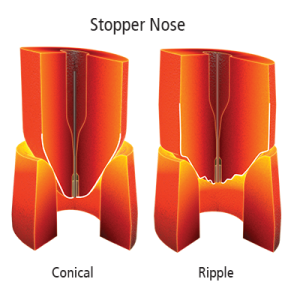
Smart Mould Level Controller
Primary objectives:
- Drive the flow valve to minimize meniscus deviation
- Self-adapt to perturbations in process
Main features:
- Decide in real time the best control strategy along casting sequence
- Minimize meniscus fluctuation when strong perturbations occur
- Auto-adapts to bulging, waves or other periodical fluctuation (option)
- Optional functions: strand Autostart, Automatic Tube Change
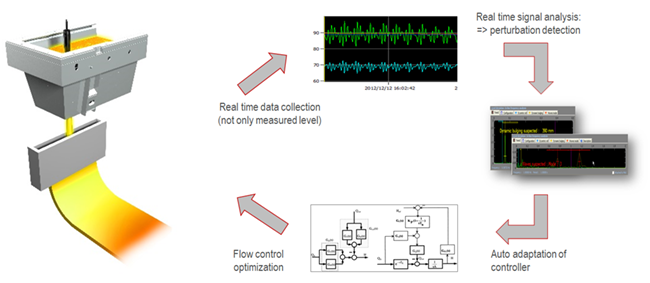
Gas Inerting
Inert Gas Control for steel protection
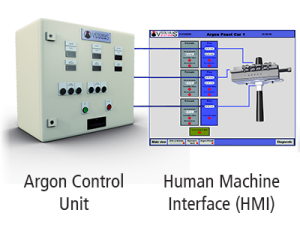
Primary objectives:
- Management of inert gas application to reduce risk of air ingression
Main features:
- Multi-channel control panel, using mass flowmeters
- Double line per loop with back pressure measurement (option)
- 3 operating modes (option): Automatic Flow Control, Automatic Pressure Control, Manual
Flux Powder
Flux Powders and Distribution Mechanisms
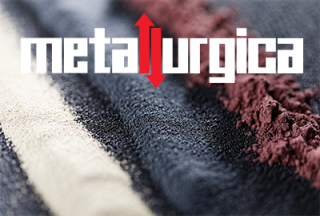
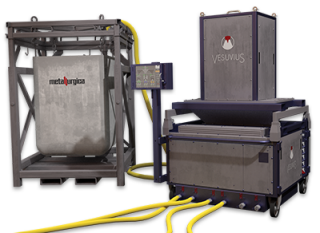
Primary objectives:
- Create lubrication layer between steel shell and mould faces,
- Protect steel top surface from re-oxidation and heat loss,
- Control heat transfer between strand & mould,
- Capture inclusions floating to top surface
- Distribute the flux regularly over the steel surface